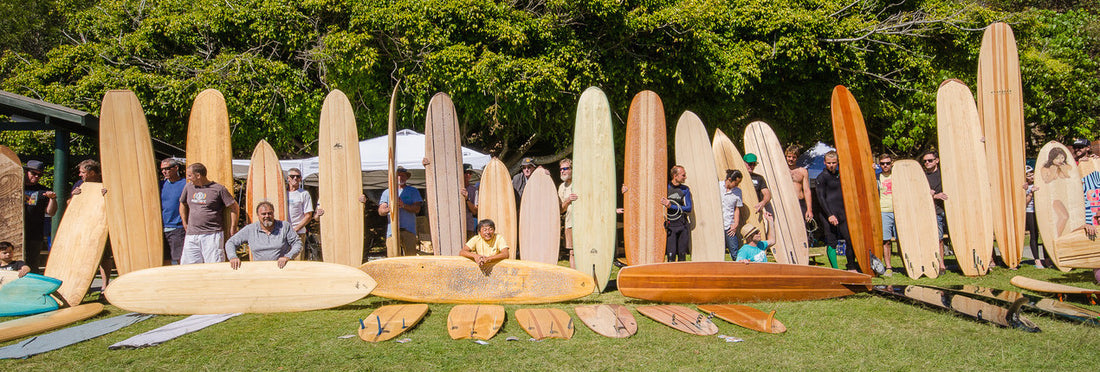
What Are Wooden Surfboards Made Of? The Most Common Woods and Materials
From the origins of surfing until now, wooden surfboards have been made from a variety of different materials. The ancient Hawaiians and Peloponnesians often used ‘Ulu’ and ‘Koa’ woods, grown in native forests local to the surf breaks where they were used. Some ancient ‘Olos’ can weigh up to 50 kgs.
In the early 20th century before the invention of foam, lighter woods became a preference. The first hollow-wooden surfboard was invented by Tom Blake in 1929 nicknamed ‘The Cigar Box’ with the goal to make lighter, more manoeuvrable surf craft.
Today the most common woods used in surfboard construction are also the lightest on earth. These are Agave (75 kg/m3), Balsa (150 kg/m3), Paulownia (280 kg/m3), Cedar (380 kg/m3), Spruce (450 kg/m3) and Redwood (450 kg/m3). Lightweight timbers are becoming more desirable for their remarkable strength to weight ratios and quick cultivation time, where trees like Balsa and Paulownia can be harvested after only 6 years of cultivated growth.
The 2 Most Common Woods
1. Paulownia
Commonly regarded as the world’s best wooden surfboard material, Paulownia is native to China and other parts of East Asia. It has a rich history and has been used extensively to make furniture, musical instruments and decorative items. They were introduced in the west in the 19th century, originally as exotic ornamental trees. Today they are also used to make surfboards.
Advantages:
- Lightweight (280 kg/m^3)
- High strength (37.8 MPa)
- Fast growing. Trees can reach a harvestable size in only 6 years
- Often considered a weed so unsustainable harvesting is unlikely
- Water resistant
- High hardness (Janka hardness 1300 N)
Disadvantages:
- Can be heavy if not crafted with enough precision
Paulownia is used in solid, skinned and hollow constructions. Companies using Paulownia wood in their surfboard construction include FireWire and ourselves, Sine Surf.
2. Balsa
Balsa wood is native to South and Central America where is was first used by indigenous people to make canoes rafts and other tools. In the past it has been used for ship building in the colonial era and to make aircraft in the world wars. Today its uses are mainly in the aerospace and marine industries, and one of them is surfboard building. Along with Paulownia, it is one of the two most used woods in surfboard construction.
Advantages:
- Lightweight (150 kg/m^3). Although often variable.
- High strength (Modulus of rupture 19.6 MPa)
- Fast growing. Trees can reach a harvestable size in only 6 years.
- Often considered a weed so unsustainable harvesting is unlikely.
Disadvantages:
- Not water resistant.
- Low Hardness (Janka Hardness 300 N). Requires significant fiberglass to reinforce.
Balsa wood is used in solid, skinned and hollow constructions. Today it is common to stumble across solid Balsa surfboards on display, often shaped into guns and longboards. Surfboard companies using Balsa wood in their construction include Varuna Surf, Kayu and Sunova.
Photo credit: Bruce Jones Surfboards
Materials Used In The 3 Wooden Surfboard Types
1. Solid Wooden Surfboards
Solid wooden surfboards are the simplest to make and consists of a sealed solid wooden core. If using Agave or Balsa wood, you will get the lightest solid wooden surfboard, but the boards will require sealing with fiberglass and resin and the wood is very fragile. Paulownia and more dense woods can be sealed more simply, with natural oils and waxes.
Approximate weights for 6’ (32L) long solid wood surfboards:
- Agave: 3.4 kg (fiberglass sealed)
- Balsa: 5.8 kg (fiberglass sealed)
- Paulownia: 9 kg
- Cedar: 12 kg
- Spruce and Redwood: 14 kg
Typical materials (by volume):
- Wood (94%)
- Wood glue (1%)
- Fiberglass and resin or oils and waxes (5%)
As you can see, solid surfboards can be very heavy, and this is why the two other construction methods are favoured today.
Photo credit: Dick Brewer
2. Skinned Wooden Surfboards
Skinned wooden surfboards are the most common type of wooden surfboard used today. It consists of a foam core, wrapped in a wood veneer (typically 2-3mm thick) and then wrapped again in fiberglass. These surfboards have a wooden appearance, although they have little sustainable advantage, as petrochemical based foams and fiberglass are still used in the construction. Although, some companies like Verdure surf are using lesser amounts of more environmentally responsible resins and cloths.
Skinned wooden surfboard can be the same weight as foam and fiberglass surfboards.
Typical materials (by volume):
- Foam (polyurethane or polystyrene) (94%)
- Wood (3%)
- Fiberglass and resin (3%)
Examples of companies using this construction method are Verdure Surf, FireWire, Aloha and Sunova.
3. Hollow Wooden Surfboards
Hollow wooden surfboards are the most complicated type of wooden surfboard to make and typically consist of a hollow wooden core wrapped in fiberglass. They are the most sustainable high-performance surfboards available on the market. Because the core is hollow, they completely eliminate the need for petroleum based foam, and depending on the wood, reduced amounts of fiberglass and resins can be used.
The weight of a hollow wooden surfboard is variable and depends on the skill of precision of the construction. Hollow wooden surfboards can be the same weight as foam and fiberglass surfboards.
Typical materials (by volume):
- Hollow wood core (96%)
- Wood glue (1%)
- Fiberglass and resin (3%)
Examples of companies making hollow-wooden surfboards include ourselves, Sine Surf, Varuna Surf and Kayu Surfboards.